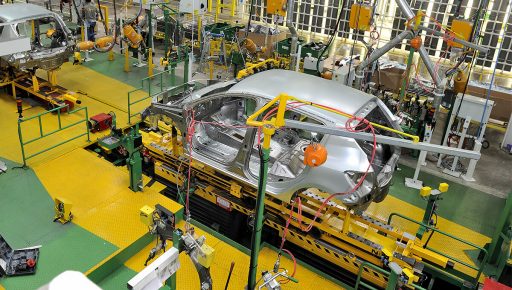
© VINCI Energies
En recueillant, analysant et exploitant les flux de données, le Manufacturing Execution System joue un rôle capital dans l’amélioration de la performance industrielle.
Ultraconnectée et génératrice d’une énorme masse de données, l’usine du futur comprend un outil essentiel : le MES (Manufacturing Execution System). Ce dernier recueille en temps réel les données liées à la production. Analysées, elles permettront d’améliorer la performance et d’optimiser la production, du lancement de commande à l’expédition du produit fini.
« Il peut s’agir de récupérer le planning de production ou les demandes de livraison, de remonter les informations du terrain sur l’état de l’installation, les ressources disponibles, les productions en cours dans les ateliers, les retards éventuels… », explique Manuel Venchiarutti, responsable d’affaires chez Actemium, la marque de VINCI Energies spécialisée dans la performance industrielle.
« En regroupant toutes les données en temps réel et au même endroit, l’analyse est simplifiée, les corrélations plus faciles à trouver pour définir, par exemple, les causes d’un retard ou d’une baisse de qualité », poursuit Laurens Marijns, consultant MES chez Actemium.
Chaque MES répond à des objectifs particuliers en fonction des besoins exprimés par l’industriel
Chaque MES répond à des objectifs particuliers en fonction des besoins exprimés par l’industriel : efficacité énergétique, respect des contraintes règlementaires ou environnementales, changement du mode de production de l’usine…
A titre d’exemple, « l’industrie automobile produit à la commande avec une très forte personnalisation de la voiture sur la ligne de fabrication, alors que des industries comme la pétrochimie fabriquent pratiquement toujours le même produit. Elles ont donc des besoins complètement différents en matière de suivi de fabrication. Dans le second cas, ils vont plutôt porter sur la limitation des rejets, la baisse des consommations d’énergie ou l’optimisation de la production », détaille Manuel Venchiarutti.
Centralisation et sérialisation
Les données générées sont centralisées dans un seul système accessible pour tous. Pour un lot précis, il est ainsi possible d’obtenir « la généalogie de tous les lots entrant dans sa composition, mais aussi les équipements sur lesquels il a été fabriqué, l’opérateur concerné, les éventuelles pannes, le détail des résultats des autocontrôles ou encore les paramètres process », détaille Jean-Michel Blanc, responsable commercial MES chez Actemium.
Pour aller plus loin, Actemium a également édité un module complémentaire permettant la sérialisation, c’est-à-dire la numérotation d’un produit de manière unique. Un outil important, alors que le besoin de traçabilité des produits est grandissant.
En facilitant la communication, mais aussi l’optimisation, la traçabilité, le contrôle de la qualité, le suivi de performance ou encore la maintenance, le MES s’inscrit comme un rouage indispensable permettant à l’usine de se transformer et de tendre vers l’interconnexion de l’industrie du futur.
12/10/2016
En savoir plus :
http://www.actemium.fr