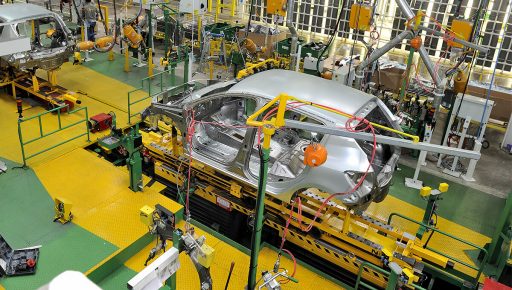
© VINCI Energies
Manufacturing Execution Systems (MES) play a critical role in improving industrial performance through data collection, analysis, and use.
The production plants of the future will be equipped with an essential tool – MES – making them hyperconnected and enabling them to generate vast amounts of data. This tool collects production data in real time. These data can be analysed to improve performance and optimise production, from ordering to shipping.
“MES can be used to retrieve production schedules and delivery requests, provide feedback on the state of the facility, the availability of resources, work-in-process on the shop floor, and potential delays,” states Manuel Venchiarutti, Business Manager at Actemium, the VINCI Energies brand specialising in industrial performance.
“By bringing together all data in real time in one place, you simplify analysis and make correlations easier to find, which helps you to determine the root causes, for example, for delays or loss of quality,” adds Laurens Marijns, MES Consultant at Actemium.
Each MES addresses specific objectives based on stated needs
Each MES addresses specific objectives based on stated needs, including energy efficiency, compliance with regulatory or environmental requirements, and changes to production methods.
To illustrate, Manuel Venchiarutti provides the following example: “The automotive industry is very responsive to customer preferences and its production lines can build cars that are highly personalised. Conversely, industries such as the petrochemical sector essentially produce the same product all the time. As a result, they have completely different needs with respect to production monitoring. In the latter case, they tend to focus on minimising emissions, reducing energy consumption, and optimising production.”
Centralization
Production-related data are centralised in a single system that is accessible to all. As a result, for any given production lot, you can obtain “the genealogy of all production inputs, information regarding the production equipment, the equipment operator, production breakdowns, results of monitoring checks, and process parameters,” states Jean-Michel Blanc, MES Sales Manager at Actemium.
In addition, Actemium has produced a module that tags each product with its own unique serial number. In light of the importance of product traceability, this is a key feature.
Thanks to its ability to facilitate communication, production optimisation, traceability, quality control, performance-monitoring, and maintenance, an MES is a must-have resource that helps to make production plants hyperconnected and future-proof.
12/10/2016
Learn more:
http://www.actemium.com