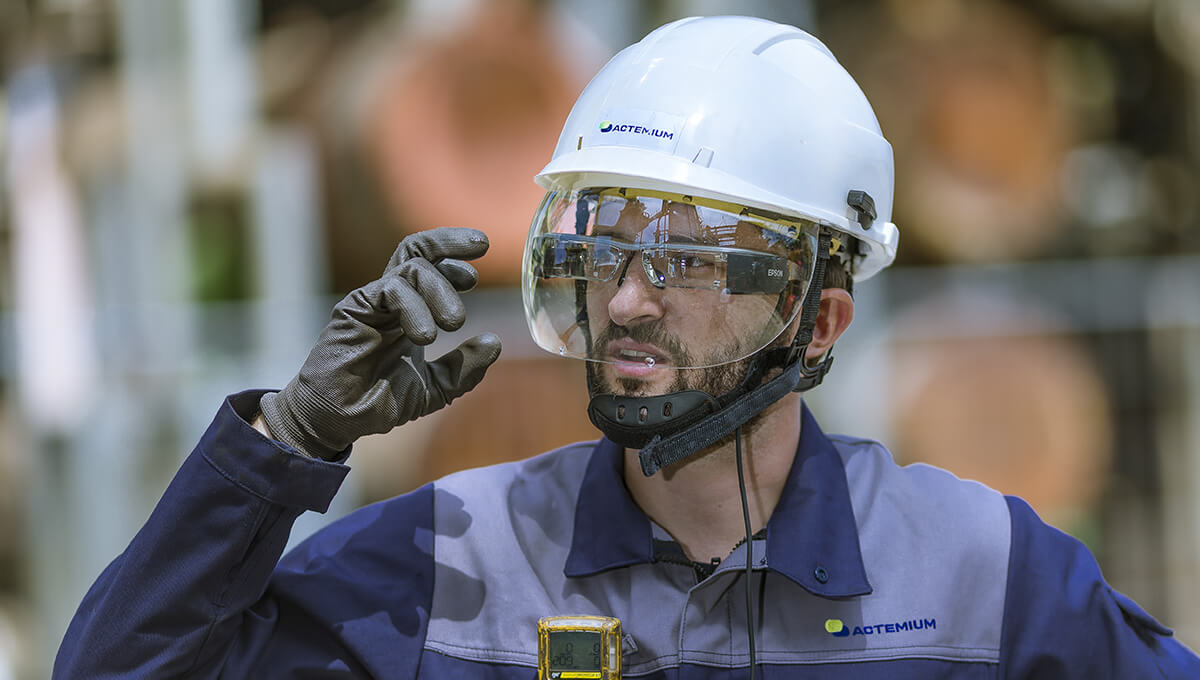
© Raphaël Soret
Actemium est partie prenante du centre d’opération à distance d’Air Liquide près de Lyon, grâce auquel l’industriel est désormais capable de « monitorer » ses unités de production en France et, demain, dans le monde entier.
Le cerveau d’Air Liquide se trouve désormais en banlieue lyonnaise, à Saint-Priest. Inauguré fin janvier 2017, le centre d’opération à distance (COD) a en effet vocation à piloter à distance la production des 22 usines françaises du groupe industriel. Collecte de données, big data et nouvelles technologies sont au cœur de ce projet d’usine du futur, dans le cadre du projet de transformation numérique d’Air Liquide, baptisé « Connect ».
Toutes les données sont centralisées. Des algorithmes sont ensuite créés, qui les analyseront et permettront d’obtenir une fréquence de panne, d’anticiper les changements de pièces.
Ajuster la consommation d’énergie
« Le premier objectif pour Air Liquide est l’optimisation de la production. Or leur activité, produire des gaz, est très consommatrice d’électricité », explique Rodolphe Letondor, chef de projet chez Actemium (VINCI Energies) qui intervient sur le projet. « Le but est donc de moduler les installations », ajoute-t-il.
Le COD peut déterminer, grâce aux données récoltées et celles issues des historiques de production collectées sur les 400 usines depuis quinze ans, si un site consomme un juste niveau d’énergie par rapport à ce dont il a besoin, pour adapter les réglages, si nécessaire.
L’optimisation ne s’arrête pas aux consommations énergétiques. En disposant d’une vue d’ensemble des sites et des besoins des clients, les opérateurs du COD adaptent le niveau de production à la demande en oxygène, hydrogène, azote et argon. Ils peuvent également arrêter ou redémarrer un site à distance.
Fiabiliser les process
L’autre objectif d’Air Liquide est d’améliorer la fiabilité de ses process grâce à la maintenance prédictive. Les données récoltées sur les sites sont analysées afin de détecter les signes avant-coureurs d’une panne ou d’un dysfonctionnement. « Toutes les données sont centralisées, aussi bien les pannes rencontrées que leur type. Des algorithmes sont ensuite créés, qui analyseront les données et permettront d’obtenir une fréquence de panne, d’anticiper les changements de pièces et les problèmes, etc. », poursuit Rodolphe Letondor.
Dans cette lignée, la maintenance et l’inspection sont simplifiées par l’utilisation de nouvelles technologies, comme les tablettes tactiles, les lunettes connectées ou les scans 3D. « Le personnel peut, au cours de sa ronde d’inspection, se connecter sur les serveurs pour obtenir des plans, avoir les informations rétroprojetées sur la visière de son casque connecté, etc. Le fait de ne pas avoir à chercher l’information facilite énormément le travail », détaille-t-il.
Si pour l’heure, seules quatre usines sont connectées, toutes devraient l’être d’ici la fin de l’année 2017, avant une deuxième phase de déploiement sur les unités de production à l’étranger.
03/07/2017