Industrie 4.0: Herausforderung kundenspezifische Massenfertigung
Lesezeit: 4 min.
Mit der Implementierung der Industrie 4.0 geht eine verfahrenstechnische Revolution einher. Dies gilt insbesondere im Automobilbau. Einige Großkonzerne, etwa der Actemium-Kunde Stellantis, sind Vorreiter auf diesem Gebiet. Die Herausforderung liegt in der Kombination von maßgeschneiderter Fertigung und Agilität.
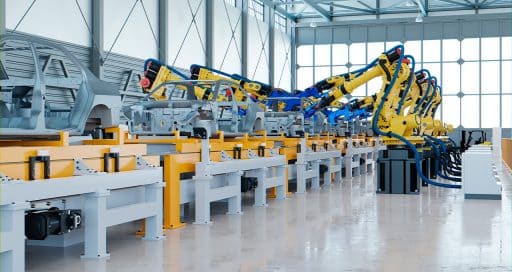
Die Fabrik 4.0 erfordert eine deutlich höhere Flexibilität und folglich eine stärkere Automatisierung bei den Fertigungsverfahren.
Das Geschäftsmodell einer Massenproduktion nach dem Motto „ein Werk, ein Produkt, ein Land“ ist überholt. Heute müssen neue industrielle Fertigungsmodelle vermeintlich die Quadratur des Kreises versuchen: Stabil mit maximaler Auslastung produzieren und gleichzeitig eine Vielzahl unterschiedlicher, individuell angepasster Waren herstellen – und das mit einer weltumspannenden Lieferkette.
Die Schaffung eines flexiblen, automatisierten und resilienten industriellen Systems: Vor dieser Herausforderung steht die Fabrik 4.0. Um sie zu meistern, ist ein neues Konzept notwendig; das der kundenspezifischen Massenfertigung. Es setzt auf eine deutlich größere Variabilität bei den Fertigungsverfahren und somit auf eine stärkere Automatisierung.
Die Autoindustrie ist in dieser Hinsicht ein interessantes Fallbeispiel. „Die wachsende Produktvielfalt und die individuelle Gestaltung (Farbe, Räder, Felgen, Oberflächen, Ledersitze, Sitzheizung usw.) erforderte die Umorganisation der Montagebänder“, bemerkt Patrick Bénard, Regionalleiter Industrie Nordostfrankreich bei VINCI Energies. Er arbeitet für den Stellantis-Konzern (Peugeot, Citroën, DS, Opel, Vauxhall, Fiat, Chrysler, Abarth, Lancia, Alfa Romeo, Maserati, Jeep, Ram, Dodge).
Die Schaffung eines flexiblen, automatisierten und resilienten industriellen Systems: Vor dieser Herausforderung steht die Fabrik 4.0.
Bisher beruhte ein Werk auf dem Grundsatz, dass die Fertigung an den Montagebändern in unterschiedliche Stationen aufgeteilt war. An jeder Montagestation gab es ein festes Team und eine Edge-of-Line-Logistik lieferte alle notwendigen Teile für die Produktion.
Neues Verfahren
Aber mit diesem Fertigungsmodell können nur ähnliche Produkte mit wenigen Varianten hergestellt werden, keine grundlegend unterschiedlichen Waren. Wie gelang die Umstellung? „2014 war die damalige PSA-Fabrik im elsässischen Mülhausen (heute Stellantis Mulhouse) eines der ersten europäischen Werke, das ein neues Fertigungsverfahren einführte“, berichtet Bénard.
„Im Grundsatz bestand es darin, dass die Teile nicht mehr einzeln per Edge-of-the-Line-Logistik geliefert, sondern bedarfsgerecht über AGVs (ferngesteuerte Transportfahrzeuge) in Form von Montagesätzen bereitgestellt wurden“, erläutert er. Diese mobilen Plattformen fahren automatisch von einem Logistikzentrum zu den Montagestationen.
Aber ein solches industrielles Fertigungsverfahren setzt eine extrem komplexe Logistik mit einem AGV-Fuhrpark in Bataillonsstärke voraus, um die zur Herstellung notwendigen Teile zum richtigen Zeitpunkt und in der richtigen Zusammensetzung an die richtige Montagestation zu befördern.
Die Lösung? „Ein sehr präzises AGV-Verkehrsmanagement“. So hat Actemium Mulhouse im Auftrag von Stellantis ein maßgeschneidertes Leitsystem entworfen, das danach in weiteren Werken in Frankreich, Spanien und der Slowakei implementiert wurde.
Seit 2012 „hat Actemium über 1.500 AGV in die Stellantis-Werke gebracht“, so Bénard. Laut dem Regionalleiter von VINCI Energies wird die zunehmend automatisierte Logistik so zu einem immer zentraleren Bestandteil der industriellen Fertigung.
Mehr Flexibilität
Die Vorteile liegen auf der Hand. „Zunächst einmal ermöglicht ein solcher Prozess kleinere Werke, weil man mehrere Modelle in mehreren Varianten auf ein und derselben Montagelinie bauen kann, die man je nach Bedarf anpasst“, erläutert Bénard.
Ein weiterer Vorteil dieses „eingleisigen“ Systems: das Werk kann im Ein-, Zwei- oder Dreischichtsystem betrieben werden, je nachdem, welche Produkte hergestellt werden. „Noch flexibler wird eine solche Fertigung, wenn man für unterschiedliche Automodelle oder -marken gemeinsame Plattformen nutzt“, fügt er hinzu.
In den Augen des Regionalleiters von VINCI Energies gehört Stellantis zu den wenigen Konzernen, die sich bereits in den Boomjahren mit der Umgestaltung ihres Fertigungsprozesses befasst haben. „Diese vorausschauende Planung war von Vorteil“, bemerkt er. „Sie steigerte die Produktivität, so dass der Konzern heute eine operative Marge von 14 % ausweist, eine der höchsten der Branche.”
16/03/2023