L’industrie 4.0 au défi de la customisation de masse
Temps de lecture : 5 min
L’industrie 4.0 annonce une révolution des process. Une révolution notamment en cours dans le secteur automobile. Certains acteurs clés sont en pointe sur le sujet, à l’image du groupe Stellantis pour lequel travaille Actemium (VINCI Energies). Enjeu : conjuguer sur-mesure et agilité.
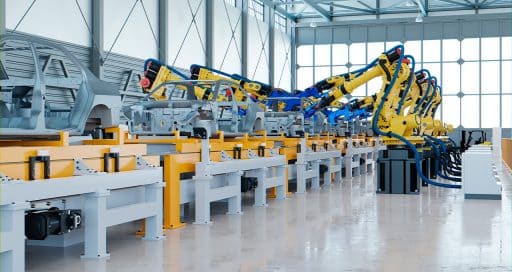
L’usine 4.0 implique une bien plus grande flexibilité des process de production, et de ce fait, une plus large automatisation.
Le modèle de production de masse basé sur le principe « un produit, une usine, un pays » est révolu. Aujourd’hui, les nouveaux modèles industriels doivent concilier l’inconciliable, ou ce qui paraît tel : produire de façon stable avec une utilisation maximale de l’outil industriel, tout en fournissant un grand nombre de produits différents et plus personnalisés, et ce, au sein d’une chaîne d’approvisionnement mondiale.
Créer un système industriel flexible, automatisé et résilient, c’est le défi de l’usine 4.0. Pour y répondre, un nouveau concept s’impose, celui de la customisation de masse. Il implique une bien plus grande variabilité dans les processus de production, et de ce fait, une plus large automatisation.
L’industrie automobile est un cas d’usage intéressant à cet égard. « La diversité croissante des produits et de leur personnalisation (couleur, roue, jante, finitions, cuir, siège chauffant…) a nécessité de revoir l’organisation des chaînes de production », note Patrick Bénard, directeur régional Industrie Nord Est chez VINCI Energies, qui travaille pour le groupe Stellantis (Peugeot, Citroën, DS, Opel, Vauxhall, Fiat, Chrysler, Abarth, Lancia, Alfa Romeo, Maserati, Jeep, Ram, Dodge).
Créer un système industriel flexible, automatisé et résilient, c’est le défi de l’usine 4.0.
Jusqu’alors, une usine était basée sur le principe de la ligne d’assemblage où les tâches sont segmentées en différentes étapes. A chacune d’entre elles, les équipes sont fixes et une logistique de bord de ligne livre tous les composants nécessaires à la fabrication.
Nouveau process
Mais ce modèle de production ne permet de fabriquer que des produits similaires avec quelques variantes, pas des produits réellement différents. Comment évoluer ? « En 2014, l’usine PSA de Mulhouse (devenue Stellantis Mulhouse) a été l’un des premiers sites en Europe à adopter un nouveau process industriel », raconte Patrick Bénard.
Le principe ? « Non plus installer les pièces au préalable en bord de ligne, mais y acheminer des kits de montage selon les besoins grâce à des AGV (véhicules à guidage automatique) », explique-t-il. Ces systèmes de plateformes mobiles se déplacent automatiquement d’un centre logistique aux stations de travail.
Mais ce procédé industriel nécessite une logistique extrêmement complexe où des bataillons d’AGV doivent apporter à la bonne station et au bon moment le juste lot de composants nécessaires à la fabrication du produit.
La solution : « une gestion très précise du trafic des AGV ». Ainsi, pour Stellantis, Actemium Mulhouse a conçu un système de supervision ad hoc qui a ensuite été déployé dans les autres usines en France, puis à l’étranger, comme en Espagne et en Slovaquie.
Depuis 2012, « Actemium a installé plus de 1 500 AGV dans les usines de Stellantis », précise Patrick Bénard. Selon le directeur régional de VINCI Energies, la logistique toujours plus automatisée est ainsi appelée à devenir un élément de plus en plus central dans la production industrielle.
Plus de flexibilité
Les avantages de ce type de process ne manquent pas. « Il permet d’abord de réduire la taille des usines puisqu’on peut produire différents modèles et variétés de produits sur une même ligne d’assemblage que l’on adapte selon les besoins », explique Patrick Bénard.
Autre avantage de « ce système en monoflux » : la possibilité d’installer une à trois équipes différentes sur la même ligne selon les produits qui doivent y être fabriqués. « Cette flexibilité est d’autant plus grande que l’on recourt aux mêmes plateformes de véhicules pour différents modèles ou marques », ajoute-t-il.
Pour le directeur régional de VINCI Energies, Stellantis fait partie des rares groupes qui ont su se poser la question de repenser leur process de fabrication quand tout allait bien. « Cette anticipation lui a été salutaire, observe-t-il. En augmentant ainsi sa productivité, le groupe affiche aujourd’hui 14 % de marge opérationnelle courante au premier semestre 2022, l’un des plus élevés du secteur. »
16/03/2023