A indústria 4.0 enfrenta o desafio da customização em massa
Tempo de leitura: 5 min
A indústria 4.0 anuncia uma revolução nos processos. Uma revolução no setor automotivo em particular. Alguns players-chave estão na vanguarda, como o grupo Stellantis, para o qual trabalha a Actemium (VINCI Energies). O desafio é combinar customização e agilidade.
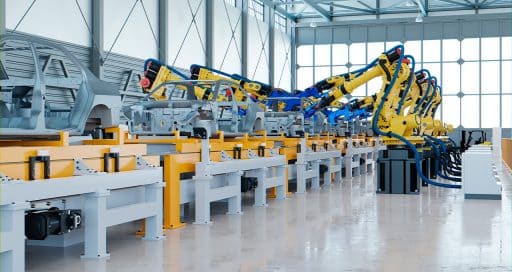
A fábrica 4.0 implica uma variabilidade muito maior nos processos de produção, portanto, uma maior automação.
O modelo de produção em massa baseado no princípio “um produto, uma fábrica, um país” está ultrapassado. Hoje, os novos modelos industriais devem conciliar o inconciliável, ou o que parece sê-lo: produzir de forma estável com a máxima utilização da ferramenta industrial, fornecendo, simultaneamente, muitos produtos diferentes e mais personalizados, e isto, dentro de uma cadeia de abastecimento global.
Criar um sistema industrial flexível, automatizado e resiliente é o desafio da fábrica 4.0. Para enfrentá-lo, é necessário um novo conceito: a customização em massa. Implica uma variabilidade muito maior nos processos de produção, portanto, uma maior automação.
A indústria automotiva é um caso de uso interessante a este respeito. “A crescente diversidade dos produtos e sua personalização (cor, roda, aro, acabamento, couro, assento aquecido, etc.) obrigou a rever a organização das linhas de produção”, observa Patrick Bénard, diretor regional Indústria Nordeste da VINCI Energies, que trabalha para o grupo Stellantis (Peugeot, Citroën, DS, Opel, Vauxhall, Fiat, Chrysler, Abarth, Lancia, Alfa Romeo, Maserati, Jeep, Ram, Dodge).
Criar um sistema industrial flexível, automatizado e resiliente, eis o desafio da fábrica 4.0.
Até então, uma fábrica era organizada em torno da linha de montagem, onde as tarefas eram segmentadas em diferentes etapas. Em cada etapa, as equipes são fixas e uma logística de bordo de linha entrega todos os componentes necessários para a produção.
Novo processo
Mas este modelo de produção só permite fabricar produtos semelhantes com algumas variações, não produtos realmente diferentes. Como evoluir, então? “Em 2014, a fábrica da PSA em Mulhouse (agora Stellantis Mulhouse) foi uma das primeiras na Europa a adotar um novo processo industrial”, afirma Patrick Bénard.
O princípio? “Não instalamos previamente as peças no bordo de linha, mas usamos AGVs (veículos guiados automaticamente) para transportar kits de montagem conforme necessário”, explica ele. Estes sistemas de plataformas móveis se deslocam automaticamente de um centro logístico para os postos de trabalho.
Mas este processo industrial requer uma logística extremamente complexa, com batalhões de AGVs que devem entregar, no posto certo e no momento certo, o lote certo de componentes necessários para fabricar o produto.
A solução: “uma gestão muito precisa do tráfego dos AGVs”. Para a Stellantis, a Actemium Mulhouse projetou um sistema de supervisão específico, que foi a seguir implantado em outras fábricas na França, e depois no exterior, como na Espanha e na Eslováquia.
Desde 2012, “a Actemium já instalou mais de 1.500 AGVs nas fábricas da Stellantis”, especifica Patrick Bénard. Segundo o diretor regional da VINCI Energies, a logística sempre mais automatizada se tornará assim um elemento cada vez mais central na produção industrial.
Mais flexibilidade
Há muitas vantagens com este tipo de processo. “Em primeiro lugar, permite reduzir o tamanho das fábricas, uma vez que diferentes modelos e variedades de produtos podem ser produzidos na mesma linha de montagem, adaptada conforme as necessidades”, explica Patrick Bénard.
Outra vantagem deste “sistema em mono fluxo” é a possibilidade de instalar uma a três equipes diferentes na mesma linha, dependendo dos produtos a serem fabricados. “Esta flexibilidade é incrementada pelo fato que são utilizadas as mesmas plataformas de veículos para diferentes modelos ou marcas”, acrescenta o diretor.
Para o diretor regional da VINCI Energies, a Stellantis é um dos raros grupos que souberam repensar seu processo de fabricação quando tudo estava indo bem. “Esta antecipação foi benéfica, observa. Ao aumentar sua produtividade desta forma, o grupo tem hoje uma margem operacional corrente de 14% no primeiro semestre de 2022, uma das mais altas do setor.”
16/03/2023