Industry 4.0 faces up to the challenge of mass customisation
Reading time: 4 min
Industry 4.0 is proclaiming a process revolution. A revolution that is well under way in the automotive sector. A number of key manufacturers are leading the way, including Stellantis, with help from Actemium (VINCI Energies). The challenge is to combine agility and bespoke production.
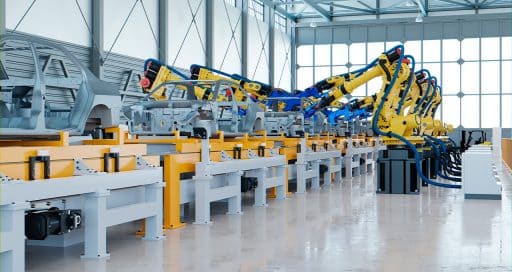
Factory 4.0 involves far greater variability in production processes, and therefore more automation.
The mass production model based on the “one, product, one factory, one country” model belongs to the past. Today, new manufacturing models have to reconcile the seemingly unreconcilable: steady production with maximised use of the production facility, while also supplying a large number of different, more customised products within a global supply chain.
The challenge of Factory 4.0 is to create a flexible, automated and resilient industry solution. In response, a new concept has emerged: mass customisation. It involves far greater variability in production processes, and therefore more automation.
Automotive manufacturing is an interesting use case in this respect. “The increasing diversity of products and customisation options (colour, wheels, rims, trims, leather, heated seats, etc.) forced us to review how we organise production chains”, says Patrick Bénard, Regional Director Industry North East at VINCI Energies, which works for the Stellantis group (Peugeot, Citroën, DS, Opel, Vauxhall, Fiat, Chrysler, Abarth, Lancia, Alfa Romeo, Maserati, Jeep, Ram and Dodge).
The challenge for Factory 4.0 is to create a flexible, automated and resilient industry solution.
Until now, a factory would follow the assembly line principle, in which tasks are segmented into different steps. Fixed teams are assigned to each of these, with line-side logistics supplying all the manufacturing components required.
New process
But this production model can only manufacture similar products with a few variants, and not truly different products. So, what is the way forward? “In 2014, the PSA plant in Mulhouse (now Stellantis Mulhouse) was one of the first sites in Europe to adopt a new industrial process”, says Patrick Bénard.
And its principle? “We stop installing parts at line side beforehand, and instead deliver assembly kits when needed using AGVs (automated guided vehicles)”, he adds. These mobile platforms move automatically between workstations in a logistics centre.
But this industrial process requires extremely complex logistics to manufacture the product, with an army of AGVs having to bring the right batch of components to the right station at the right time.
The solution is “Extremely precise management of AGV traffic”. For Stellantis, Actemium Mulhouse addressed this by designing an ad hoc supervision system that was immediately deployed in the other facilities in France, then rolled out overseas, for example in Spain and Slovakia.
Since 2012, “Actemium has installed more than 1,500 AGVs in Stellantis plants”, says Patrick Bénard. According to the VINCI Energies regional director, increasingly automated logistics is becoming more and more central to industrial production.
Greater flexibility
There are many advantages to this type of process. As Patrick Bénard explains, “Firstly, it allows us to reduce the size of factories, because we can produce different models and varieties of products on a single assembly line that is adapted according to requirements”.
Another advantage of this “single-flow system” is the possibility of installing between one and three different teams on the same line depending on the products that need to be made. “This flexibility is even greater when the same vehicle platforms are used for different models or marques”, he adds.
For the VINCI Energies regional director, Stellantis is one of those rare groups to have undertaken a redesign of their manufacturing processes when everything was working well. “This forward thinking has proven highly beneficial”, he observes. “By increasing productivity in this way, the group now boasts an operating margin of 14% for the first quarter of 2022, one of the highest in the sector”.
16/03/2023