Die Märkte werden immer anspruchsvoller und erfordern zunehmend mehr Engineering in den Produktionsanlagen. Hier das Beispiel von einem großen Automobilhersteller und von Actemium in Deutschland.
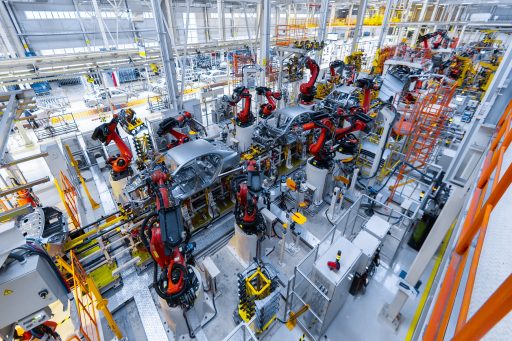
Mit der Entwicklung hyperagiler Produktionsmodelle, die sich flexibel an Kundenerfordernisse anpassen, schlägt die Geschichte der Industrie ein neues Kapitel auf.
Es handelt sich um eine der großen Verheißungen der Digitalisierung in der Industrie: eine schneller reagierende Industrieproduktion zur Herstellung individuellerer Erzeugnisse. Zunehmend volatile Märkte und anspruchsvolle Kund:innen erzeugen einen Druck, unter dem die Industrie ihre Prozesse der Nachfrage anpassen muss. Das erfordert eine Umgestaltung der Produktionslinien.
Die individualisierte Produktion steht am Ende einer langen Evolution der industriellen Fertigung. Noch in den 1950er Jahren zielte das ursprünglich von Henry Ford konzipierte System auf die Massenfertigung von Standardprodukten ab. Dreißig Jahre später bediente das Toyota-Modell noch immer Massenmärkte, allerdings mit einer Just-in-Time-Fertigung. Es war der Beginn der „Lean Production“, bei der die Kundin oder der Kunde eine Reihe zusätzlicher Optionen bestellen und so das Produkt teilweise individualisieren konnte.
Mit der Entwicklung hyperagiler Produktionsmodelle, die sich flexibel an die Kundenanforderungen und die vielfältige Nachfrage anpassen, tritt die Industrie aktuell wieder in eine neue Phase ein – im Business-to-Business-Bereich (BtoB) genauso wie im Business-to-Consumer-Geschäft (BtoC).
Auf Abruf und maßgeschneidert
Die Individualisierung kann unterschiedliche Formen annehmen: Produktion auf Abruf (on Demand) oder nach Maß. Im ersten Fall startet die Produktion erst nach einer Bestellung. Hergestellt und montiert wird also nur das, was tatsächlich bereits verkauft ist – Verkaufsprognosen spielen für die Fertigung keine Rolle mehr. Dieses System hat erhebliche Vorteile: Begrenzte bzw. nicht vorhandene Lagerbestände, keine Ladenhüter mehr, kürzere Lieferzeiten, schnelle Markteinführung von Produkten und Innovationen (Time to Market), Möglichkeit zu Markttests vor Kapazitätserweiterung.
Die individualisierte Produktion steht am Ende einer langen Entwicklung der industriellen Fertigung.
Bei der Produktion nach Maß wird ein einzigartiges Produkt nach Kundenvorgaben gefertigt. Dieser Ansatz hat den großen Vorteil, dass eine enge Kundenbindung entsteht und wertvolle Marketingdaten gesammelt werden können. Er entwickelt sich insbesondere in Bereichen wie der Brillenherstellung und der Mode schnell weiter.
Ob auf Abruf oder nach Maß – in beiden Fällen geht es darum, den Bedarf der Kund:innen mit einem mehr oder weniger individualisierbaren Angebot zu erfüllen, Produktionskosten durch Robotereinsatz zu senken und für eine agilere Fertigung zu sorgen.
Retrofit bei großem deutschen Automobilhersteller
Um ihre volle Wirkung zu entfalten, muss auch im Vorfeld der eigentlichen Fertigungsprozesse auf industrielle Agilität geachtet werden, bis hin zur Anordnung und Funktionsweise der Produktionslinien und -abläufe. Dafür ist erhebliches Know-how im Engineeringbereich erforderlich.
Das jüngste Beispiel eines großen Autoherstellers veranschaulicht diese Entwicklung. Der deutsche Konzern hat umfangreiche Sanierungs- und Umbauprojekte an einigen Produktionsstandorten angestoßen.
In einem Werk bei Stuttgart wurde die automatische Fördertechnik in der Lackiererei komplett umgestellt. Beim elektrischen Retrofit, das von Actemium Guebwiller Handling Systems und Actemium Mulhouse Plant Solutions übernommen wurde, ging es um die elektrische und sicherheitstechnische Ertüchtigung und Modernisierung der Produktionslinien.
Das Lastenheft, das den beiden Business Units von VINCI Energies vorgelegt wurde, enthielt eine organisationstechnisch kritische Klausel: Antriebe, Drehzahlregler und Schaltschränke mussten im laufenden Betrieb getauscht werden.
Neue Montageplattform
Einige Kilometer von Baden-Baden entfernt wird bei dem Autohersteller ein noch komplexeres Projekt umgesetzt. Ab 2024 will er neue Fahrzeuge auf den Markt bringen. Dafür soll das Werk mit einer neuen Plattform ausgestattet werden.
„Wir wurden mit der Anpassung von vier großen Teileströmen beauftragt: Räder, Sitze, Mechanik, Vorder- und Hinterachse. Das erfordert Kompetenzen im Bereich Systemintegration, Handling und Elektrotechnik, die Einbeziehung des kompletten Umfelds (Hängebahnen, Förderbänder, Laufstege) und die Erfassung aller störenden Elemente, die demontiert oder geändert werden müssen“, erläutert Patrick Benard, Leiter von VINCI Energies France Industrie Nord Est.
Der Auftrag von Actemium umfasst Planung, Realisierung, Montage und Inbetriebnahme von zwei Fertigungslinien. Der Beginn der Vorproduktion ist für September 2023 geplant, die Serienproduktion soll 2024 anlaufen, wobei bis 2027 weitere Fertigungslinien in Betrieb gehen werden.
16/05/2023