Industrial agility: a prerequisite for “Production as a Service”
Reading time: 4 min
In response to increasingly challenging markets, manufacturers are having to re‑engineer their production lines. We look at examples involving Actemium and a major car manufacturer in Germany.
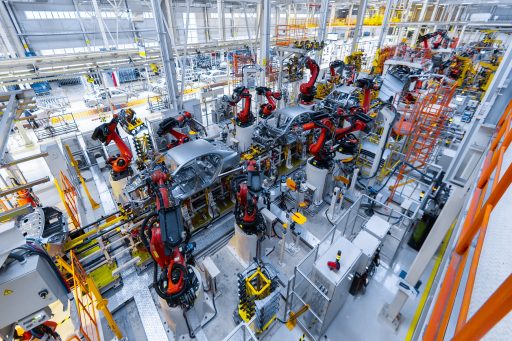
A new chapter opens in the history of manufacturing with the development of hyper-agile production models able to meet individual customers’ requirements.
One of the big promises of digital transformation in the manufacturing world is that it will enable businesses to become more responsive and develop increasingly customised products. Under pressure from increasingly volatile markets and ever more demanding customers, manufacturers need to match their processes more closely with demand. But this requires changes to their production lines.
Custom production has emerged from the long process of evolving manufacturing models. In the 1950s, the Ford system aimed to produce standardised goods for a mass audience. Thirty years later, the Toyota model continued to target mass markets, but with a focus on lean manufacturing. This was the birth of “lean”, which allowed the customer to choose a partly customised product from a range of options.
Today, a new chapter is beginning in the history of manufacturing, with the development of hyper-agile production models able to meet individual customers’ requirements (flexibility) and diverse demand (reconfiguration). This applies to business-to-business and business-to-customer scenarios alike.
On-demand and bespoke production
Customisation can combine different formats: on-demand production and bespoke production. With the former, production begins only when an order is confirmed. Manufacture and assembly are reserved for products that have actually been sold, rather than working to sales forecasts. This system offers significant advantages: low or non-existent stocks, zero risk of unsold products, accelerated execution, short time-to-market for products and innovations, and the ability to test markets before increasing capacities.
Custom production has emerged from the long process of evolving manufacturing models.
Bespoke production, on the other hand, involves creating a unique product from scratch to the customer’s specifications. This approach, which offers major benefits in creating an intimate relationship with the customer and facilitating the collection of valuable quantities of marketing data, is taking hold rapidly in sectors like fashion and eyewear.
Whether on demand or bespoke, both approaches are based on satisfying customers’ needs with a more or less customisable product, reducing production costs through automation, and making production more agile.
Retrofit at a major car manufacturer in Germany
To be comprehensive, industrial agility must be implemented upstream of the manufacturing processes themselves, extending even to the layout and operation of production lines and flows. Of course, this requires advanced engineering expertise.
The recent example of a major car manufacturer in Germany neatly illustrates this trend. The German group has undertaken major renovation and reconfiguration projects at several of its production sites.
At its plant, not far from Stuttgart in Baden‑Württemberg, Germany, automated handling lines in the paint workshops have been totally transformed. Actemium Guebwiller Handling Systems and Actemium Mulhouse Plant Solutions were engaged for the electrical retrofit operation to update these production lines to meet the latest safety standards.
The brief handed to the two VINCI Energies business units included a critical organisational clause: the motors, variators and cabinets had to be replaced during active production.
New assembly platform
Also in Germany, the car maker has an even more complex project under way near Baden‑Baden. From 2024, it will be bringing new vehicles to market and therefore needed to equip its factory with a new assembly platform.
“We were brought in to adapt the four main auxiliary flows: wheels, seats, mechanical engineering, and front and rear axles”, says Patrick Benard, Head of VINCI Energies France Industrie Nord Est. “This task combining systems integration, surveying, materials handling and electrical engineering required us to consider the whole environment (fixing supports, conveyors, catwalks, etc.) and identify any elements interfering with these to be dismantled or modified”.
Actemium’s role was to design, build, assemble and commission two lines. The pre-production startup phase will begin in September 2023, with full production expected to start in 2024, and new launches continuing until 2027.
16/05/2023