L’agilité industrielle, prérequis pour une production « as a service »
Temps de lecture : 6 min
Pour répondre à des marchés de plus en plus exigeants, les industriels doivent d’abord engager des travaux d’ingénierie sur leurs lignes de production. Exemple avec un grand constructeur automobile et Actemium en Allemagne.
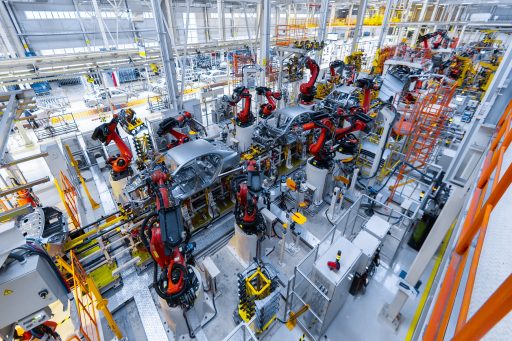
Le développement de modèles de production hyperagiles, adaptés à la demande de chaque client, ouvre une nouvelle page de l’histoire industrielle.
C’est l’une des grandes promesses de la transformation digitale dans le monde industriel : permettre aux entreprises de gagner en réactivité afin de développer des offres plus personnalisées. Face à la pression de marchés de plus en plus volatils et de clients de plus en plus exigeants, les industriels doivent en effet rapprocher leurs process de la demande ; ce qui nécessite d’adapter leurs chaînes de production.
La production personnalisée procède d’une longue évolution des grands schémas industriels. Dans les années 1950, le système fordiste s’attache à produire des biens standardisés pour un public de masse. Trente ans plus tard, le modèle toyotiste vise toujours des marchés de masse, mais avec une production au plus juste. C’est le lancement du « lean », grâce auquel le client peut choisir, par le jeu des options, un produit en partie customisé.
Aujourd’hui, c’est encore une nouvelle page de l’histoire industrielle qui s’ouvre avec le développement de modèles de production hyperagiles, adaptés à la demande de chaque client (flexibilité) ainsi qu’à la diversité de la demande (reconfiguration). Et ce, en business-to-business (BtoB) comme en business-to-consumer (BtoC).
A la demande et sur mesure
La personnalisation peut épouser des formats différents : production à la demande ou production sur mesure. Dans le premier cas, la production n’est lancée que lorsqu’une commande est confirmée. On ne fabrique ou on n’assemble que ce qui sera effectivement vendu et non ce que dictent les prévisions de vente. Ce système présente des atouts de poids : stocks limités, voire inexistants, risques d’invendus éliminés, délais d’exécution accélérés, rapide mise sur le marché des produits ou des innovations (time to market), possibilité de tester des marchés avant d’augmenter les capacités.
La production personnalisée s’inscrit dans la longue évolution des grands schémas industriels.
La production sur mesure consiste, elle, à créer de toutes pièces un produit unique, conforme aux spécifications du client. Cette approche, qui a le grand mérite de créer une relation d’intimité avec le client et de collecter une quantité précieuse de données à des fins marketing, se développe rapidement dans des secteurs comme la lunetterie ou la mode.
A la demande ou sur mesure, dans les deux cas, il s’agit de satisfaire les besoins des clients avec une offre plus ou moins personnalisable, de baisser le coût de production grâce à la robotisation et de rendre la fabrication plus agile.
Rétrofit chez un grand constructeur automobile en Allemagne
Pour être complète, l’agilité industrielle doit s’inviter en amont des procédés de fabrication eux-mêmes, jusque dans les choix d’agencement et de fonctionnement des chaînes et des flux de production. Une condition qui requiert des expertises pointues en ingénierie.
L’exemple d’un grand constructeur automobile ces derniers mois illustre ce mouvement. Le groupe allemand a ainsi engagé d’importants chantiers de rénovation et de reconfiguration de certains de ses sites de production.
Au sein de l’usine dans la région du Baden-Württemberg, près de Stuttgart, les ateliers de peinture ont subi une transformation totale des lignes de manutention automatisée. L’opération de rétrofit électrique, confiée à Actemium Guebwiller Handling Systems et Actemium Mulhouse Plant Solutions, a consisté à mettre les lignes de production aux derniers standards en intégrant les normes de sécurité les plus récentes.
Le cahier des charges soumis aux deux entreprises de VINCI Energies comprenait une clause organisationnelle critique : il fallait remplacer les moteurs, les variateurs et les armoires pendant la période de production.
Nouvelle plateforme d’assemblage
Toujours en Allemagne, à quelques kilomètres de Baden-Baden, c’est un projet plus complexe encore qui est en train de s’opérer chez le constructeur automobile. A compter de 2024, il mettra sur le marché de nouveaux véhicules et, pour ce faire, l’entreprise a souhaité doter son usine d’une nouvelle plateforme.
« Nous avons été mandatés pour adapter les quatre grands flux annexes : roues, sièges, mécanique, trains avant et arrière. Un travail d’ensemblier, d’expertise, de manutention et d’ingénierie électrique qui nécessite une prise en compte de tout l’environnement (structures d’accrochage, convoyeurs, passerelles) et le recensement de tous les éléments interférents à démonter ou à modifier », explique Patrick Benard, directeur VINCI Energies France Industrie Nord Est.
L’intervention d’Actemium comprend l’étude, la réalisation, le montage et la mise en service de deux lignes. Le démarrage en préproduction aura lieu au mois de septembre 2023, la production en série devrait débuter courant 2024 avec des lancements jusqu’en 2027.
16/05/2023