Monoprix worked with Actemium to mechanise e-commerce order preparation, pooling inventory, halving delivery times, and improving the process.
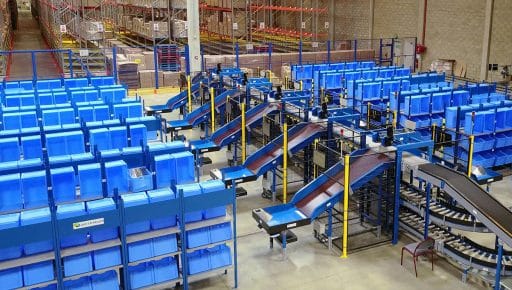
© VINCI Energies
The Monoprix brief was clear-cut. “We wanted to bring the e-commerce and store distribution systems together at the same site so as to pool our inventory and simplify logistics. This would avoid limiting our inventory to a single sales stream, and enable us to control our entire supply chain,” says Laurent Badetz, Director of Methods and Organisation at Monoprix logistics subsidiary Samada. “Order preparation, which was managed by an outside provider, was therefore brought in-house to our national site in Combs la Ville.”
Process mechanisation was entrusted to Actemium (VINCI Energies). “Buildings, customer requirements, production speeds, and locations are always different. As an integrator, we select the elements for each individual installation, tailoring it to the customer’s needs. We put together the technological components, the standard parts,” says Clément Schmitt, project manager at Actemium Lyon Logistics.
Scalable system
In this case, Actemium was called on to install the system within an existing building, that continued to operate during the works, and to complete the project within a two-month timeframe (corresponding to the interval between two fashion seasons). “E-commerce changes very quickly, so the system was designed to be scalable, with a current production rate of 2,200 items per hour that can be increased,” says Clément Schmitt.
In addition to better inventory management, the new system meets a further goal specific to the sector: it improves the customer’s time to market. “The solution Actemium proposed enabled us to halve our delivery times to two days, and improved the quality of order processing,” says Laurent Badetz.
“The solution proposed by Actemium enabled us to halve our delivery time and improved the quality of order processing.”
To achieve this objective, Actemium installed an order preparation system based on mass collection that can handle a large number of orders at the same time, and an efficient, rapid sorting system.
The Actemium Lyon Logistics project manager adds, “We have developed a sorting table technology that achieves the desired speed and provides the flexibility required for e-commerce while processing the products without damaging them. It meets process speed requirements while remaining within a limited budget, unlike larger sorting systems such as Cross-Belt and Push Tray, which are expensive and more cumbersome to install.”
Ergonomic studies
Actemium also carried out ergonomic studies of sorting tables. “We built prototypes of the tables to validate working heights, tray weights and heights, etc. We then did a study of the locations of the various system components, conveyor belts, etc. and installed and commissioned the system at the customer’s premises,” says Clément Schmitt.
“At Monoprix, mechanising the logistics system was our first experience. It opens the door to future work. Actemium was able to work out the investment corresponding to what we wanted to do and to our flow of merchandise. We achieved our objectives in terms of cost, quality, and delivery time from the start,” says Laurent Badetz, Director of Methods and Organisation at the Monoprix logistics subsidiary.
17/10/2017