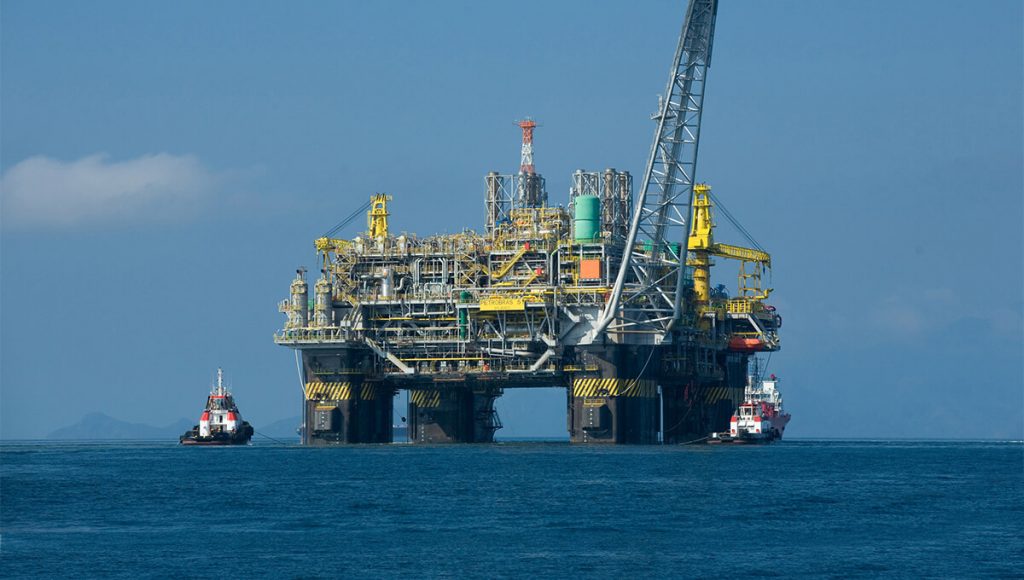
© DR
The oil industry is looking to optimise platform operating costs. Revisiting its maintenance methods will help drive performance.
The recession has forced the oil industry to address an important issue: that of optimising barrel production costs and consequently, platform operating costs. Revisiting its maintenance methods gives it the leverage needed to meet this objective.
Achieving a significant impact on operating costs means innovating on an organisational level rather than on a technical one: “Encouraged by our clients, we changed our approach to maintenance, moving from a system where crews are based offshore 100 per cent of the time, towards a system of resource pooling, where workers are based onshore. We form client-dedicated crews that can operate across several sites in a given area,” explains Jimmy Neron, Commercial Director at VINCI Energies Oil & Gas.
Advance scheduling and engineering
Offshore maintenance is performed over shorter periods, in campaigns, with much of the scheduling and engineering work completed in advance. “By preparing preventive or corrective maintenance tasks onshore, we optimise the amount of time spent on operations offshore and the presence of mobile crews on site,” he adds.
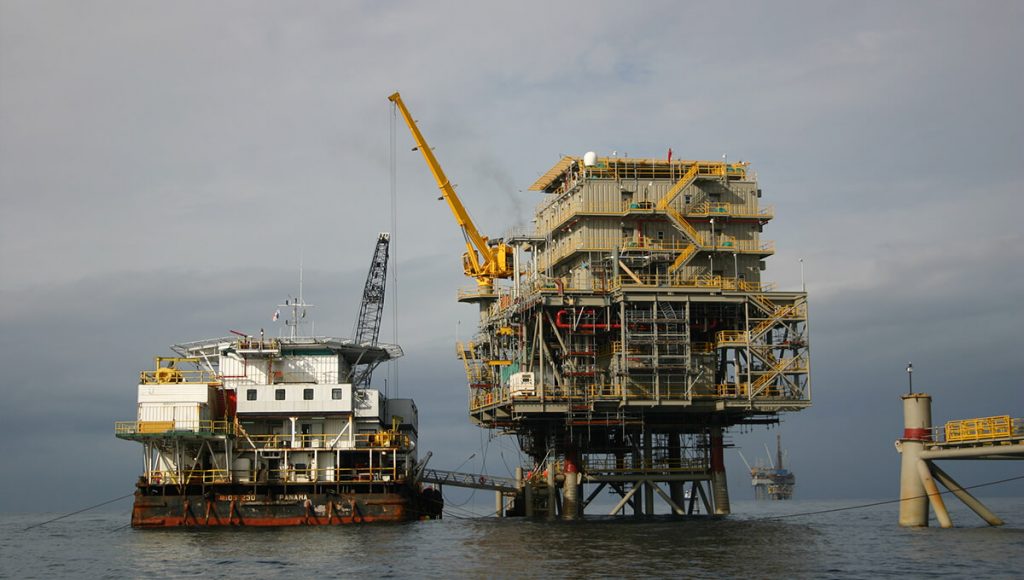
© DR
In Angola, for example, VINCI Energies is responsible for maintaining two FPSOs (Floating Production, Storage and Offloading units), Girassol and Dalia, on Block 17 for Total E&P Angola. “Together with Total, we revamped the organisation of the ad hoc crews who operate on the two vessels. So if there is a need for an HVAC specialist on Dalia and another on Girassol, then the tasks are planned accordingly and the worker operates on both FPSOs,” says Jimmy Neron.
This resource pooling and reorganisation method has generated “maintenance savings of 25 to 30 per cent for the client. In terms of personnel, there has been a 30 per cent reduction in the number of permanent workers on board Girassol. Instead of 92 people, there are now 49, with 15 working on rotation throughout the year,” points out Jimmy Neron.
“Our methods and performance in terms of multi-technical maintenance and services rendered have proved their worth.”
This new way of organising work to make it more efficient involves many changes: it means reorganising jobs, having more method & operation teams onshore, and monitoring indicators and tasks. A virtual operational room, replicating the offshore control room, was therefore created. Dubbed the “smart room” at Total, this facility makes it possible to share the same information in real-time and to monitor all indicators and tasks.
“Our methods and performance in terms of multi-technical maintenance and services rendered have proved their worth, to the extent that clients who don’t normally operate this way are now showing an interest in the model. We hope to extend the expertise we have gained in Angola – and the other countries in which we operate like Nigeria, Congo and Cameroon – to new clients in the coming months,” concludes Jimmy Neron.
16/02/2017