Low code provides agile solution for accelerating reindustrialisation
Reading time: 5 min
The reindustrialisation of a country like France hinges on automating production lines. However, a severe lack of programming skills is hampering the process. The solution may be to develop low-code applications.
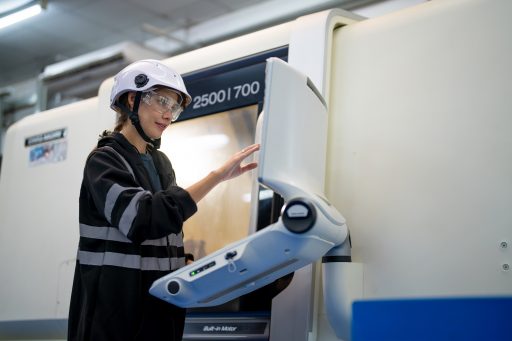
Industrial factory employee working in metal manufacturing industry
In the space of a few years, the manufacturing sector has harnessed a range of leading-edge technologies to enhance the operational and economic performance of its production lines. Artificial intelligence, augmented reality, 3D printing and developments in data are just some examples. By integrating ever more intelligence into their factories, businesses are better able to analyse, understand, measure, anticipate and adapt their processes.
But in the future, investment in industrial innovation may be guided by another aim. Employers will face serious hiring pressures, if not talent shortages, in a number of professions: cargo handling, engineering, computer programming, painting and welding. One of the more seriously explored avenues to plug this skills gap is automation.
“The reindustrialisation of France will not happen without an acceleration of automation.”
Until now the deployment of robots has been seen mainly as a way to reduce physically demanding work for operators. Today, it also addresses the crucial issue of industrial sovereignty. “Reindustrialisation will not happen in France without an acceleration of automation,” says Frédéric Boulvert, innovation business engineer at Actemium Rennes and coordinator of the advanced robotics working group at the Actemium Robotics Club.
If there are to be more robots in workshops and on production lines, then the scope of the trades and tasks they are assigned to will need to be expanded. Programming skills will therefore be required to ensure that robots are versatile, in line with an as-a-service industrial production approach.
An “agnostic” system
This means mobilising resources in order to train engineers and technicians in programming languages that become rapidly obsolete. To avoid giving up in the face of a severe skills shortage, businesses will need to transition gradually towards low-code or, at a later date, no-code automation.
So what is this technology? It enables operators to customise functional requirements themselves and to teach robots to meet these requirements using offline software applications. With low code or no code, you no longer need to be an IT expert to show robots what “movements” to recreate.
Although the main manufacturers of industrial robots (FANUC, KUKA, ABB, Stäubli) already sell applications that allow their machines to be designed, optimised, simulated and programmed offline, “these are mainly proprietary solutions for use by robots of the same brand,” notes Frédéric Boulvert.
A manufacturer that equips its production lines with robots from different brands will have to invest in as many software programmes or licences and consequently make provision in its budgets for training.
There is therefore a market need for more open, technology- and vendor-agnostic solutions like Robcad from Germany’s Siemens, DELMIA Robotics from France’s Dassault Systèmes, RoboDK from Canada’s RoboDK, KMeleon from France’s Tesseract Solutions and D:PLOY from Denmark’s OnRobot.
Some solutions even aim to make industrial robotics as widely accessible as possible, for use say in short-run or single-item production, processes that are hard to automate because of high costs.
General-purpose solutions
“Most low-code or no-code robot applications on the market today are geared towards business functionality, whether that is palletising, welding, part cleaning or waste management,” points out Frédéric Boulvert. For example the Actemium Le Mans Intégration design office has developed a bin-picking* solution that can be used to determine the positioning of the various bulk components in a single bin and pick them up.
However, general-purpose solutions are also emerging. At the beginning of 2023 Paris start-up Fuzzy Logic Robotics announced that it was making its no-code robotic programming and simulation software available online, along with documentation and training tutorials.
Isn’t this acceleration in the deployment of low-code (and soon no-code) robot applications on production lines likely to overshadow the profession of integrator? “The use of heavy-duty robots will always require expertise like ours, especially in terms of maintenance. And offline applications will quickly generate new needs – a market we will legitimately target,” says Frédéric Boulvert.
*A technology applied in the manufacturing sector to move components so that they can be used in subsequent production stages.
16/06/2023